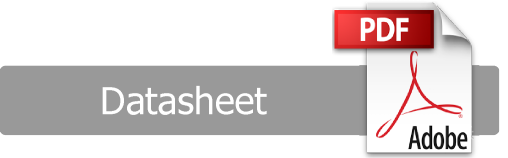
Malt roasters
These production units are designed for the production of caramel and coloring malts used in breweries or in other branches of food industry. Malt roasters belong to auxiliary components of malt-producing line and work in cycles according to a selected mode of roasting. The roasting machine is the heart of the whole production unit. The equipment of roasting plant includes malt cooling, sophisticated system for flue-gas and culm aspiration, product storage and recording, packing, dispatch, as well as flue-gas recuperation or combustion of aromatic substances. Each customer’s requirements are considered individually and each roasting plant as a whole is designed completely anew. Basic and most frequently demanded versions of the roaster are as follows:
Malt roaster PS 800
- malt roaster capacity per cycle: 800 kg in caramel malt
- number of cycles in 24 hours: 4 - 6 (depending on the type of caramel)
- annual output: 850 - 1.250 tons
- basic dimensions of roaster: 5.250 x 2.250 x 3.350 mm
Malt roaster PS 1000
- malt roaster capacity per cycle: 1.000 kg in caramel malt
- number of cycles in 24 hours: 4 - 6 (depending on the type of caramel)
- annual output: 1.000 - 1.800 tons
- basic dimensions of roaster: 5.600 x 2.650 x 3.450 mm
Malt roaster PS 2000
- malt roaster capacity per cycle: 2.000 kg in caramel malt
- number of cycles in 24 hours: 4 - 6 (depending on the type of caramel)
- annual output: 2.100 - 3.100 tons
- basic dimensions of roaster: 6.700 x 3.100 x 3.900 mm
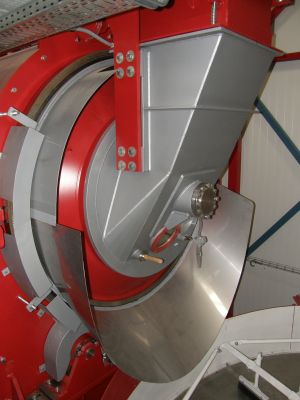
Malt roaster PS 1000
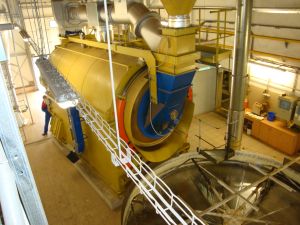
Malt roaster PS 2000
Malt plant and brewery designs
Malt is the crucial raw material for beer production and is produced in malt plants. A malt plant is a complex of technological units where grain (barley, wheat, rye, etc.) is gradually converted into malt. The malting process itself is much the same in small maltings (producing only tens of tons per annum) as well as in large-scale industrial malt plants (producing hundred tons a day). Even though the production of malt is a very old, in a way quite conservative process, the new findings in recent years (brought about by development in computer technologies, construction materials, diagnostics and other branches of science) are being implemented profusely in designing and construction of malt plants. Malt as such can be produced with relatively simple equipment in a bigger garage as well as on extensive, several-acre premises with complex treatment of intake, processing and storage of input material, through malting process proper up to storage and dispatch of variegated final products. Each malt plant is a peculiar, irreproducible original that unlike other industrial branches (such as automobile production) evades serial design.
We believe that the long-term experience of our team in this field gives a convincing quality guarantee to our customers.

Malt plant
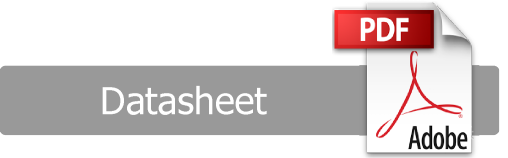
Micromalting plant
This sophisticated laboratory equipment is used for grain cultivation, most frequently for test malting of barley. Its control and data output is fully automated. It is an indispensable supplement to any modern malting facility and is utilized in colleges and research institutes.
Micromalting plant M-3BX
- dimensions of one technological box: 1.155 x 645 x 1.050 mm
- weight of one technological box: max. 175 kg
- total installed input: 4,7 kW
- required water inlet parameters: pressure 0,3 - 0,6 MPa, consumption 10 litres/min
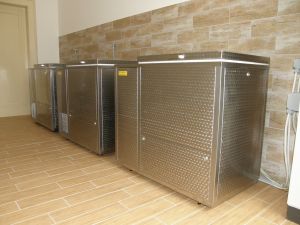
Micromalting plant
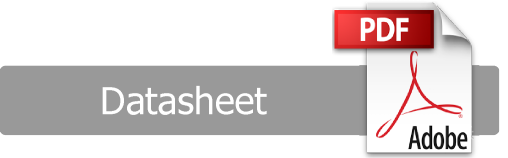
Malt mill
This single-purpose machine is designed for milling and crushing raw malt. It is used in smaller breweries to give essential treatment to malt in the brewhouse; in large breweries the machine is utilized for auxiliary milling of special malts. The basic version may be supplemented with hopper feeding or milled malt transport to the brewhouse.
Malt mill MS 160/160
- capacity: 250-450 kg malt per hour
- installed input: 1,5 kW
- weight including hopper and stand: approx. 250 kg
2016 | Zábřeh na Moravě (Czech Republic) |
---|---|
2015 | Prague (Czech Republic), Hanoi (Vietnam) |
2012 | Strzegom (Poland), Jerevan (Armenia), Praha (Czech Republic), Sao Paulo (Brazil) |
2008 | Dvůr Králové nad Labem (Czech Republic) |
2006 | Hanoi (Vietnam) |
2005 | Makhachkala (Dagestan) |
2003 | Saigon (Vietnam), Dětenice (Czech Republic) |
2001 | Makati City (Philippines), Ulanbatar (Mongolia), Saigon (Vietnam) |
2000 | Vranje (Serbia), Orel (Russia) |
1999 | Tashkent (Uzbekistan), Dushanbe (Tadzikistan), Kagoshima-Ken (Japan) |
1998 | Odesa (Ukraine) |
1997 | Kagoshima (Japan), Dražič (Czech Republic), Moscow (Russia), Kusano (Japan), Hamamatu (Japan), Vladikavkaz (Russia), Glazov (Russia), Kagoshima-Ken (Japan), Pivo Praha, Prague (Czech Republic) |
1996 | Trnava (Slovakia), Svidník (Slovakia), Kiev (Ukraine), Tokyo (Japan), Saratov (Russia), Osijek (Croatia), Arnstad (Germany), Golzow (Poland), Gdańsk (Poland) |
1995 | Mostarez Moscow (Russia), Sochi (Russia), Ongidao (China), Ongidao (China), Kirishima Higrand, Brevery Ltd. (Japan), Zheleznogorsk (Russia), Moku Moku (Japan), Yamato (Japan), Dakovo (Croatia), Tolun (Russia), Hodonín (Czech Republic), Rýmařov (Czech Republic), Ústí Nad Labem (Czech Republic), Průhonice (Czech Republic) |
1994 | Ryazan (Russia), Siumbras A.S. Kaunas (Lithuania), Koneisto – Norge (Norway) |
1993 | Azo Severodoneck (Ukraine), Orenburg (Russia), Novosergievka (Russia), Sibnefteprovod (Tyumen autonomous district, Russia), Azot Cherepovec (Russia) |
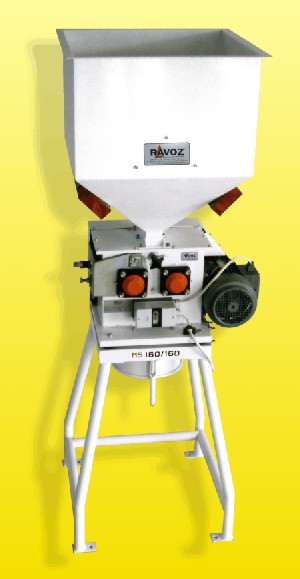